Mastering the Art of Metal Fabrication: Your Ultimate Guide to Die Casting Machine Parts
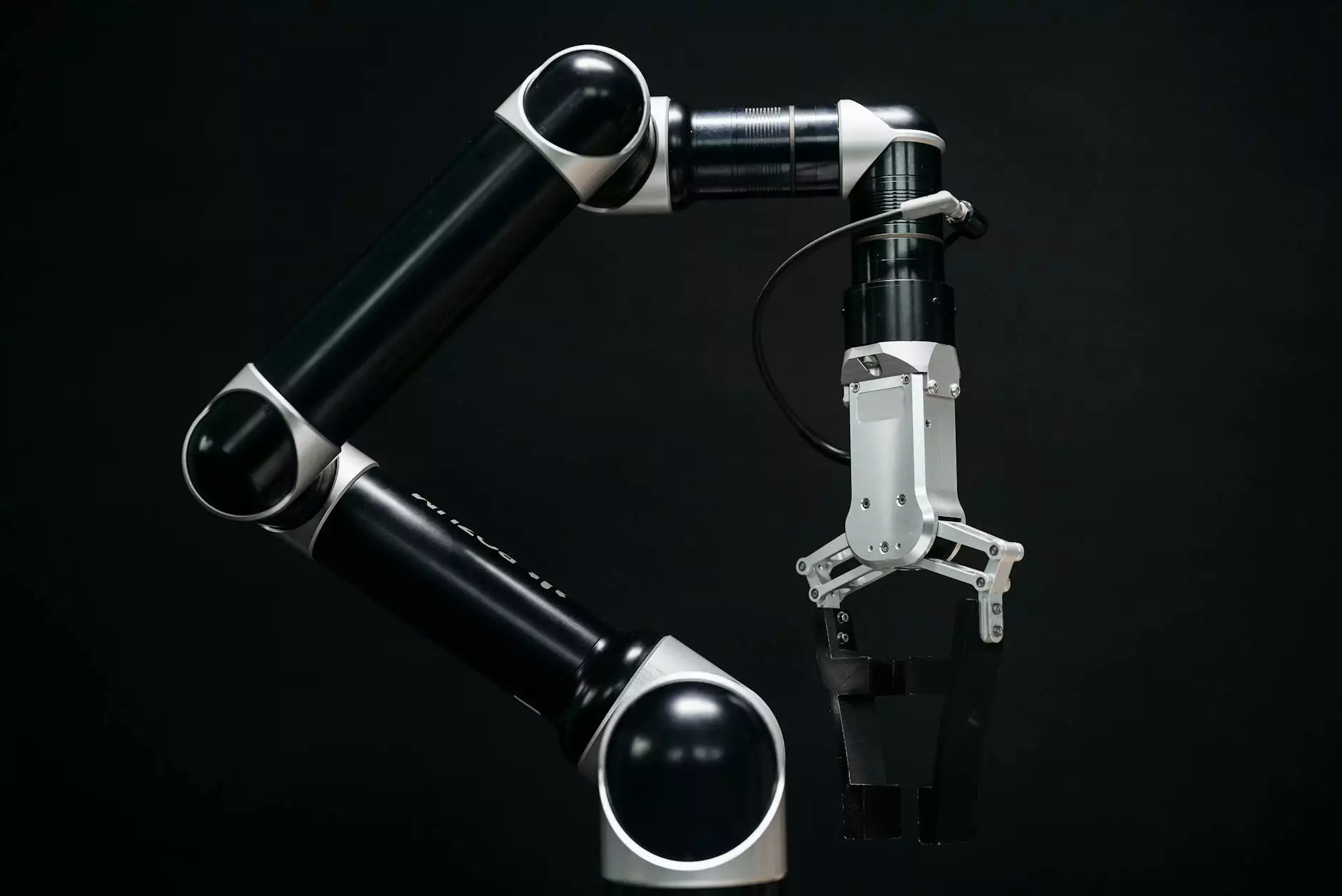
In today's competitive manufacturing landscape, the importance of precision, quality, and innovation cannot be overstated. For companies involved in metal fabrication, especially those specializing in die casting machine parts, understanding the intricacies of production processes, material selection, and technological advancements is crucial for maintaining a competitive edge. DeepMould stands at the forefront of this industry, offering unparalleled expertise as a leading metal fabricator dedicated to delivering high-precision components that meet the highest standards.
Understanding Metal Fabrication: The Foundation of Modern Manufacturing
Metal fabrication is a broad term encompassing a variety of processes used to transform raw metal materials into finished products. From cutting, bending, and assembling to welding and finishing, each step requires specialized skills and equipment. The goal is to produce durable, functional, and cost-effective components tailored to specific industrial applications.
For companies engaged in the production of die casting machine parts, mastering these processes ensures the ability to create complex geometries with tight tolerances. Metal fabrication also involves continuous innovation, such as adopting new materials and advanced machinery, which directly influence the quality and performance of the final products.
Why Choose DeepMould for Metal Fabrication of Die Casting Machine Parts
DeepMould has built an outstanding reputation as a reliable metal fabricator specializing in manufacturing high-precision die casting machine parts. Our commitment to quality, technological excellence, and customer satisfaction sets us apart from competitors. We utilize cutting-edge machinery, including CNC machining centers, automation, and quality control systems, to ensure each component meets stringent industry standards.
Our team of skilled engineers and technicians brings decades of experience in metalworking and die casting industry best practices, guaranteeing the delivery of parts that are not only precise but also durable under demanding conditions.
The Critical Role of Die Casting Machine Parts in Manufacturing Efficiency
Die casting machine parts serve as the backbone of high-volume manufacturing processes, enabling the mass production of complex metal parts with exceptional accuracy. These components include die casting molds, ejector pins, guide pins, sleeves, cores, and various structural elements vital for the machine's operation.
High-quality die casting machine parts directly impact the efficiency, product quality, and lifespan of casting equipment. Poorly manufactured parts can lead to increased downtime, higher maintenance costs, and defective castings. Therefore, choosing a dependable supplier like DeepMould ensures that your machinery operates flawlessly and produces consistent, defect-free products.
Technologies and Materials Used in Manufacturing Die Casting Machine Parts
Advanced Manufacturing Technologies
- CNC Machining: Enables complex geometries with high precision, ensuring that each part fits perfectly and functions efficiently.
- EDM (Electrical Discharge Machining): Used for creating intricate shapes and fine details necessary for specialized die casting components.
- Heat Treatment: Enhances mechanical properties such as hardness, toughness, and wear resistance, extending the lifespan of die casting parts.
- Surface Finishing: Processes like polishing, coating, and plating improve corrosion resistance and reduce friction, vital for movable or exposed parts.
- Automation and Inspection Systems: Utilize machine vision and AI for real-time quality control, reducing errors and ensuring consistency across large production runs.
Materials Utilized in Manufacturing Die Casting Machine Parts
Material selection plays a pivotal role in determining the durability and functionality of the parts. Common materials include:
- High-Speed Steel (HSS): Known for its toughness and wear resistance, ideal for cutting tools and ejector pins.
- Stainless Steel: Provides excellent corrosion resistance, suitable for parts exposed to harsh environments.
- Aluminum Alloys: Lightweight and easy to machine, often used for guide pins and sleeves where weight reduction is beneficial.
- Zinc and Magnesium Alloys: Common in low-pressure die casting, offering good machinability and strength.
Quality Assurance in Manufacturing Die Casting Machine Parts
To achieve optimal performance, metal fabricators must implement rigorous quality control protocols during every stage of the manufacturing process. This includes:
- Material Inspection: Ensuring raw materials meet industry standards before processing begins.
- Process Monitoring: Real-time data collection during machining to maintain tight tolerances.
- Dimensional Inspection: Utilizing Coordinate Measuring Machines (CMM) to verify geometric accuracy.
- Surface Testing: Check for imperfections such as cracks, porosity, or surface irregularities.
- Final Testing: Load testing or operational checks to confirm that parts perform under real-world conditions.
At DeepMould, quality assurance is embedded into our manufacturing philosophy, ensuring each die casting machine part is reliable and durable, minimizing operational risks for our clients.
Customization and Design Flexibility in Die Casting Machine Parts
Every application has unique requirements. As such, customization in die casting machine parts is essential for achieving specific functional goals. Our manufacturing capabilities include:
- Design Optimization: Using CAD/CAM software to refine part geometries for better performance and manufacturability.
- Material Tailoring: Selecting or developing alloys that meet specific strength, wear resistance, or thermal requirements.
- Prototyping: Rapid manufacturing of prototypes for testing and validation before mass production.
- Cost-Effective Solutions: Balancing quality and expenditure to deliver competitive pricing without compromising standards.
Our team collaborates closely with clients to understand their needs, offering tailored solutions that enhance the efficiency and lifespan of their die casting machinery.
The Future of Metal Fabrication and Die Casting Parts
With the rapid advancement of technology, the future of metal fabrication and die casting machine parts is poised for even greater innovation. Emerging trends include:
- Additive Manufacturing (3D Printing): Introducing new possibilities for complex, lightweight, and optimized components.
- Smart Materials: Developing alloys with embedded sensors or self-healing capabilities to enhance performance.
- Automation and IoT: Integrating Internet of Things (IoT) for real-time monitoring and predictive maintenance, reducing downtime.
- Sustainable Manufacturing: Emphasizing eco-friendly processes and recyclable materials to minimize environmental impact.
DeepMould is committed to staying ahead of these trends, investing in research and development to provide state-of-the-art die casting machine parts that meet future industry needs.
Conclusion: Elevate Your Manufacturing with Quality Metal Fabricator Solutions
In conclusion, the manufacturing of die casting machine parts is a highly specialized field requiring expert knowledge, advanced technology, and strict quality standards. As a pioneering metal fabricator, DeepMould continuously strives to deliver innovative solutions that empower businesses to enhance their productivity, reduce costs, and improve product quality.
Whether you need custom die casting components, precision machined parts, or comprehensive manufacturing support, choosing a partner dedicated to excellence is vital. Contact DeepMould today and discover how our expertise can help drive your manufacturing success.