Unveiling the Power of Plastic Injection Products
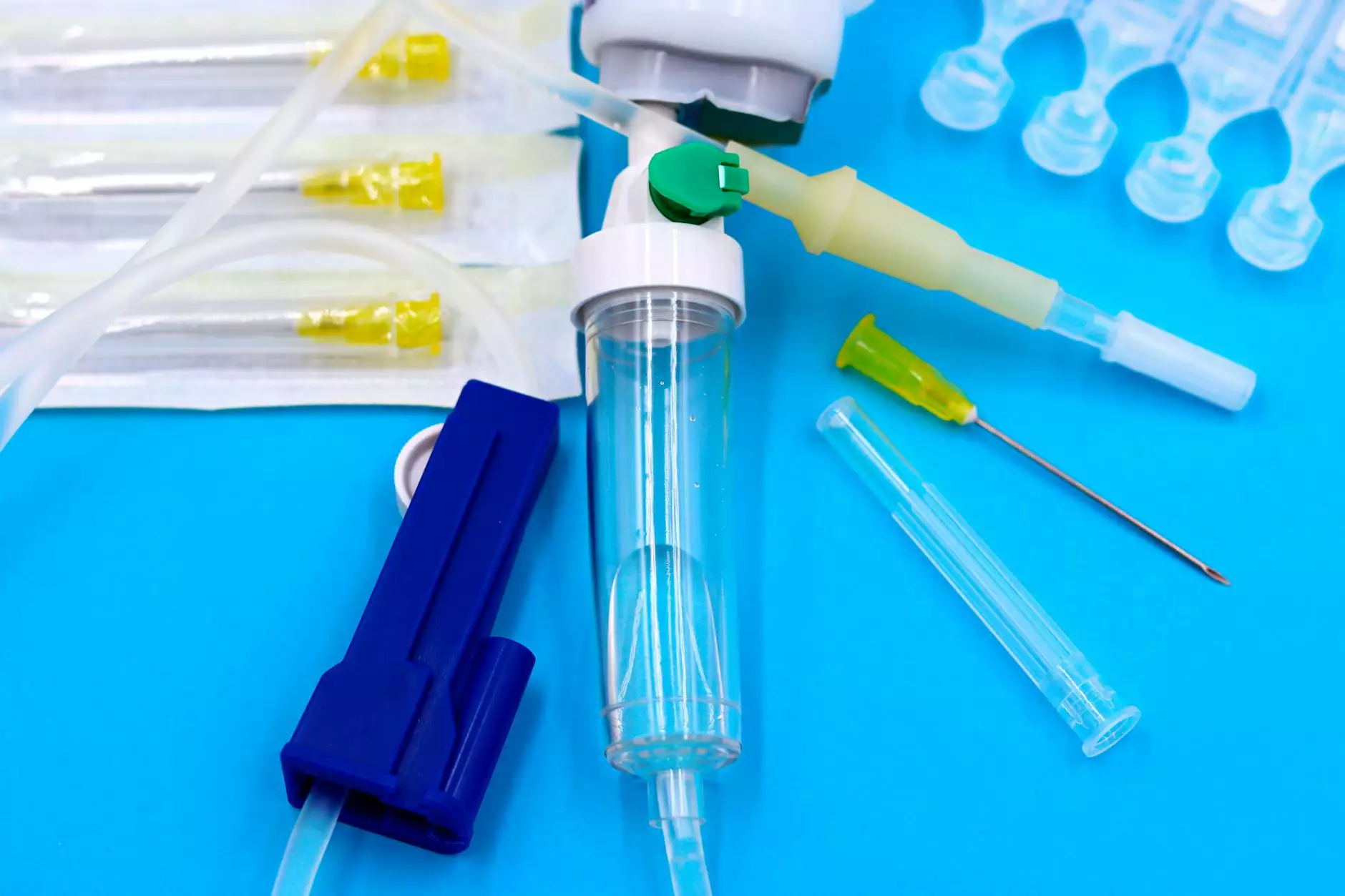
The realm of plastic injection products has transformed the manufacturing landscape, allowing companies to create a multitude of components with precision and efficiency. In this comprehensive article, we will delve into what plastic injection molding is, its advantages, the process involved, and how it stands unmatched in creating high-quality industrial products.
Understanding Plastic Injection Molding
Plastic injection molding is a manufacturing process used for creating parts by injecting molten plastic into a mold. This method is prevalent in various industries, including automotive, medical, aerospace, and consumer goods, due to its ability to produce complex shapes with fine details.
How Does Plastic Injection Molding Work?
The process of plastic injection molding involves several key steps:
- Design: The first stage is designing the product and its mold using CAD software. This design phase sets the blueprint for the end product.
- Mold Creation: A precision mold is crafted from durable materials. The mold is typically made from steel or aluminum and must endure high pressure and temperature.
- Plastic Melting: Plastic pellets are heated until they melt into a viscous liquid. This molten plastic is then ready for injection.
- Injection: The molten plastic is injected into the pre-heated mold cavity under high pressure, filling the cavity and allowing the material to take shape.
- Cooling: After injection, the molten plastic cools and solidifies within the mold, maintaining the desired shape.
- Ejection: Once the product has cooled sufficiently, it is ejected from the mold, ready for further processing or finishing.
The Benefits of Investing in Plastic Injection Products
Businesses looking to optimize their production processes can reap numerous benefits from plastic injection products. Here are some pivotal advantages:
1. High Efficiency and Speed
One of the most significant advantages of plastic injection molding is its speed. Large quantities of products can be manufactured quickly, often with minimal human intervention.
2. Reduced Waste
Plastic injection molding minimizes material waste. The excess material can often be recycled and reused, which is beneficial for both the environment and the company's bottom line.
3. Consistency and Precision
The automated process ensures that each product is produced consistently, maintaining tight tolerances for precision components that require exact measurements.
4. Versatility
Plastic injection molding can produce a vast array of products, from intricate parts used in medical devices to robust components in heavy machinery. This versatility makes it a preferred choice across industries.
5. Cost-Effective for Large Productions
While the initial setup cost of molds can be high, the ability to produce large batches quickly and with minimal waste makes the overall cost per unit very competitive.
6. Design Flexibility
With advanced technology and materials, designers can create complex shapes and intricate designs that would be challenging or costly to achieve through other manufacturing methods.
Applications of Plastic Injection Products
The applications of plastic injection products are vast and varied, significantly impacting numerous sectors.
Aerospace Industry
In the aerospace industry, precision parts made from lightweight plastics are critical for improving fuel efficiency and overall performance of aircraft. Components such as valve covers and interior fixtures often utilize injection-molded plastics.
Medical Devices
The medical field heavily relies on plastic injection products for manufacturing devices that require strict adherence to hygiene and dimensional accuracy. Examples include syringes, surgical instruments, and housings for diagnostic equipment.
Consumer Products
Everyday products like containers, toys, and kitchenware often employ plastic injection molding due to its capacity to produce durable and aesthetically appealing items at scale.
Automotive Sector
The automotive industry benefits greatly from injection molded parts used in dashboards, bumpers, and interior fittings, enhancing both the performance and design of vehicles.
Electronics
Injection molding is also essential in the electronics industry for creating covers, casings, and components that require both strength and aesthetics, such as mobile phones and laptops.
Why Choose Sumiparts for Your Plastic Injection Needs?
When considering suppliers for plastic injection products, it is essential to partner with a reputable company that values quality and service. Sumiparts exemplifies excellence in the following ways:
Quality Assurance
Sumiparts is committed to providing high-quality plastic injection products that meet or exceed industry standards. Each manufacturing process undergoes rigorous quality checks to ensure reliability and safety.
Expertise and Experience
With years of experience in the industry, Sumiparts has honed its processes to deliver the best results. Their team of experts understands the nuances of plastic injection molding, ensuring every project is managed with precision.
Custom Solutions
Understanding that each business has unique needs, Sumipartsoffers customized solutions tailored to meet specific project requirements, from design to production.
Comprehensive Service Range
Beyond plastic injection, Sumiparts provides extensive industrial supplies across categories such as machining, laser cutting, welding, and vulcanization, making them a one-stop shop for all industrial needs.
Conclusion
In summary, plastic injection products represent a cornerstone of modern manufacturing, offering businesses unparalleled efficiency, precision, and versatility. By choosing a reliable provider such as Sumiparts, companies can leverage these benefits to ensure their products stand out in a competitive marketplace. As industries continue to evolve, the significance of high-quality plastic injection components will only increase, making it essential for businesses to invest wisely for sustained growth and innovation.